Auxano® Technology
Discontinuous Surface Topology, Engineered for a Continuous Bony Interface
Auxano® is transforming the orthopedic industry by enhancing hard tissue integration and redefining the bone-implant interface across various implant types. As a leading platform technology, Auxano® brings orthopedic professionals closer to personalized implants tailored to individual anatomies. This innovation supports advancements in minimally invasive surgery (MIS), enabling faster, more efficient procedures with minimal hardware and simplified joint preparation.
At Auxano® Medical, we prioritize safety, effectiveness, and surgeon collaboration to deliver state-of-the-art orthopedic solutions. Our evolving designs offer continuous fixation interfaces, optimized stress transfer, comprehensive fixation options, and seamless compatibility with advanced fabrication technologies. Explore how Auxano® is setting new standards in orthopedic implant design and surgical innovation.
Continuous Fixation Interface
Efficient Stress Transfer
Primary & Secondary Fixation
Fully Engineered Solution
Technology Compatibility
Fabrication Compatibility

Continuous Fixation Interface
Current Problem
Negative features in porous implants require bone to grow along tortuous paths that are not interconnected, resulting in a discrete “discontinuous phase” of bone. Some porous surfaces have displayed incomplete bone migration to the base of the implant interface.
Auxano® Solution
How Does Auxano® Do It?

Efficient Stress Transfer
Current Problem
The order of magnitude difference in material properties between bone and metals used in orthopedic implants has plagued the industry for decades.
Auxano® Solution
How Does Auxano® Do It?
The Auxano® technology allows greater control of the bone volume percent at the bone-implant interface by varying pillar spacing, size, length, and material characteristics.

Efficient Stress Transfer
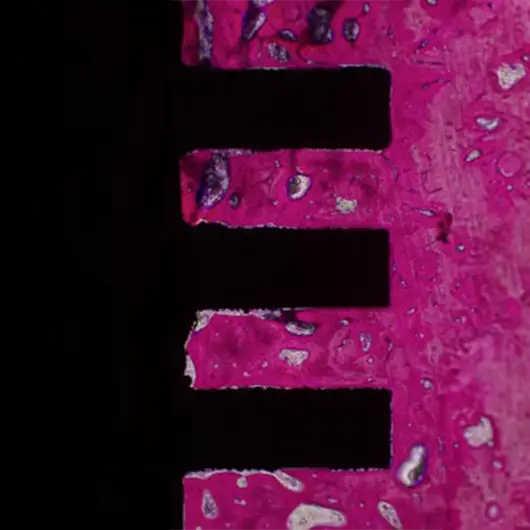
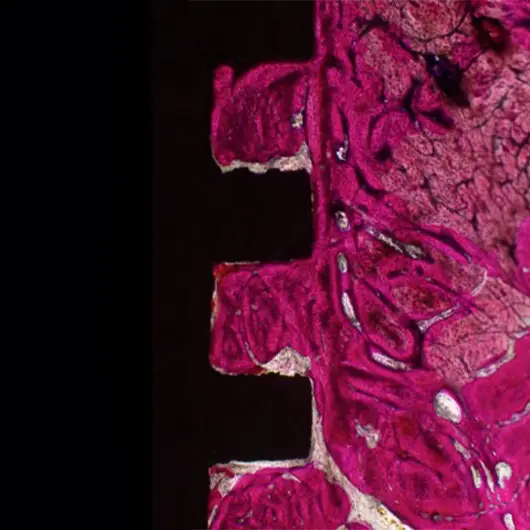
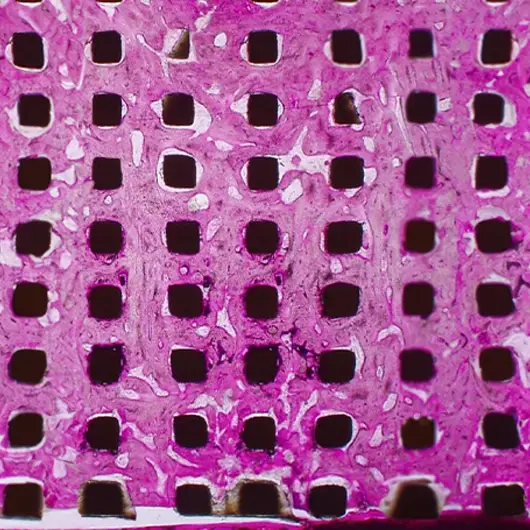
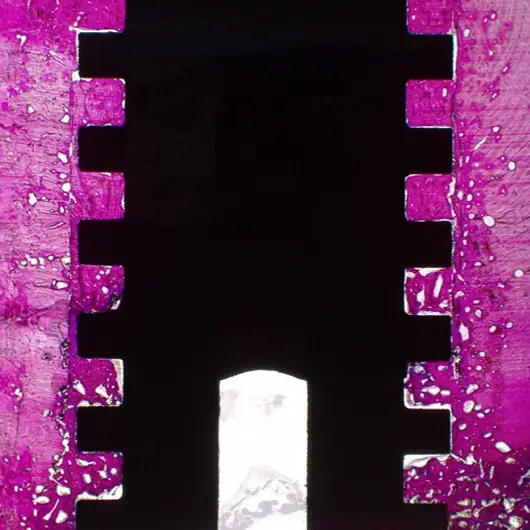
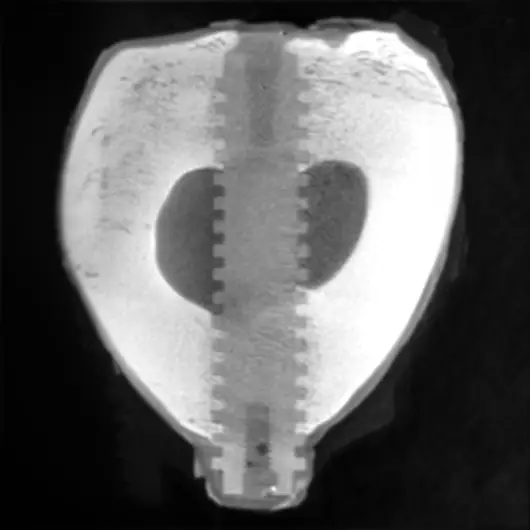
Primary & Secondary Fixation
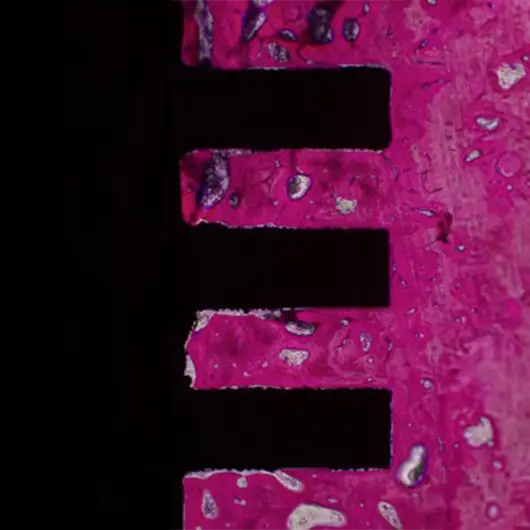
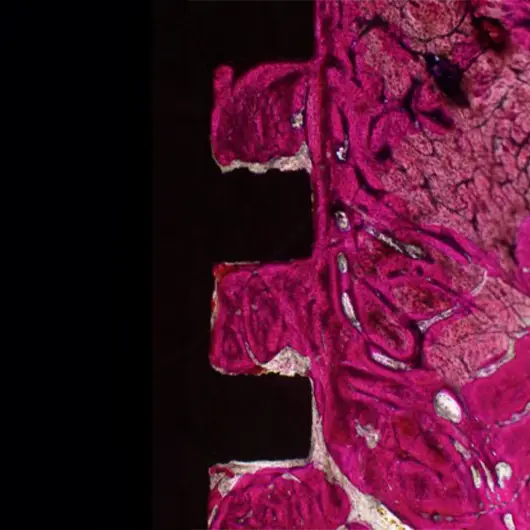
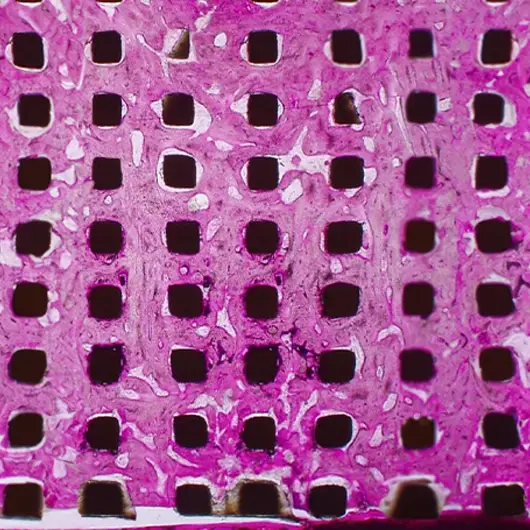
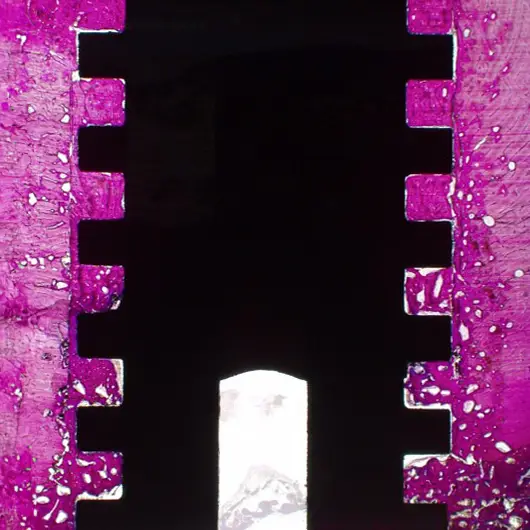
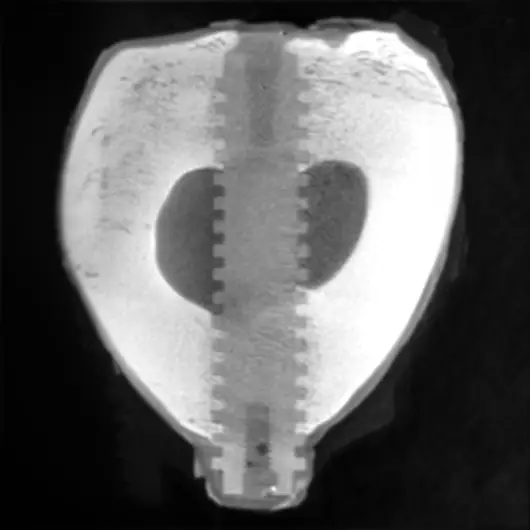
Primary & Secondary Fixation
Current Problem
Non-union, implant loosening, and implant infection are the top causes of failure in orthopedic devices. Primary and secondary fixation at the bone-implant interface is where these failed devices struggle to fulfill the desired outcome.
Auxano® Solution
How Does Auxano® Do It?

Fully Engineered Solution
Current Problem
Each location in the body brings about different local loading conditions and bone anatomy. There is a need to have control over the implant surface to account for the variability in these conditions.
Auxano® Solution
How Does Auxano® Do It?

Fully Engineered Solution

Technology Compatibility
Current Problem
Many surface technologies can only be applied on their own when an application may require a combination of surface morphologies to elicit the desired cellular response.
Auxano® Solution
How Does Auxano® Do It?

Fabrication Compatibility
Current Problem
A large percentage of the commonly used surface technologies are only compatible with certain substrate materials made using specific fabrication techniques.
Auxano® Solution
How Does Auxano® Do It?
